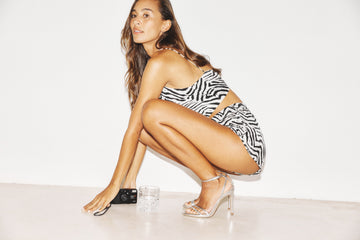
Custom designed prints are one of the many ways we like to add diversity to our brand. Our graphic design team has a very diligent design process when it comes down to creating prints for new collections and styles that everyone will love. Our newest Daydream Collection features a custom Tiger Print that was made from start to finish. Some of our favorite styles that come in the Tiger Print are the Zuri Set and the Farrah Swimsuit.

The first step in this design process is researching upcoming trends and color ways that can somehow work with a collection that we’re already working on or finding a print that's strong enough to base a collection off of. We like to use all sorts of tools to gain inspiration when it comes down to designing our prints. One of my personal favorites is traveling and getting inspired by nature. Sometimes certain unique plants or a color scheme in the sky will turn the light bulb in my mind on and all I want to do is doodle it out until I get something that would make a good print. Another one of my favorite tools is by falling down a deep tunnel of pinterest and make a mood board. When it comes to print designing for clothing, some of the things I keep in mind is coming up with something that would be flattering on all body shapes and sizes, and finding a middle ground between too out there and something that’s not too boring.

Once I know what I’m going for, I’ll grab my iPad and start doodling away. I switch between using my Procreate on my iPad or using my computer for Adobe Illustrator, most of the time I end up using both of them. I’ll start with a rough sketch of the print that I’m going for, playing around with different sizing, shapes, colors and all of that fun stuff. Once you start to draw it out and see it in real life, you get a better idea of what works and what doesn’t. Once I get a good draft of my print, sometimes I’ll just clean it up in another layer on Procreate, and other times I’ll take it into Illustrator and really make sure everything is precise. The most important step of all of this is turning the print into a repeat pattern! If it’s not a repeat then you would see the end/start of the print on the styles you print it on and it would just not look cute. I like to do this by taking it into Photoshop and making it into a repeat that fits exact to the printing size.

We incorporate different printing techniques depending on the materials we will use since not all printing techniques are suitable and delivers the best quality. For example, for all of our swimsuits we incorporate digital printing on recycled nylon fabric for a high quality finish that will not fade. This type of print is like printing the design from the computer directly on the fabric and is a digitized technique compared to another technique we use which is more traditional called ‘screen printing.’ In this technique the artwork is transformed into a wooden screen that has two sizes depending on how big of the material we need to transfer the print to. For a repeat pattern such as our new tiger print, we typically transfer the artwork to a screen that is 1 meter by 2 meter and then it is all printed on the fabric manually. The fabric is laid flat on a long table and the print engineers move the screen with precision to print the pattern repeatedly without breaking it. And they do this on meters and meters of fabric and this process takes skill and time to complete. After that, the fabric is left to air dry so that the print settles into the fabric beautifully like it did with the Zuri Top and Zuri Shorts. We only implement hand screen print technique on the styles that use silk and ECOVERO™.
If you ever have any questions please feel free to email us or send us a DM on instagram.
Related Articles